Are your issues similar? Visit our Case Studies page with new insights to uncover value centered solutions to shared automation challenges.
Case studies – Just in case!
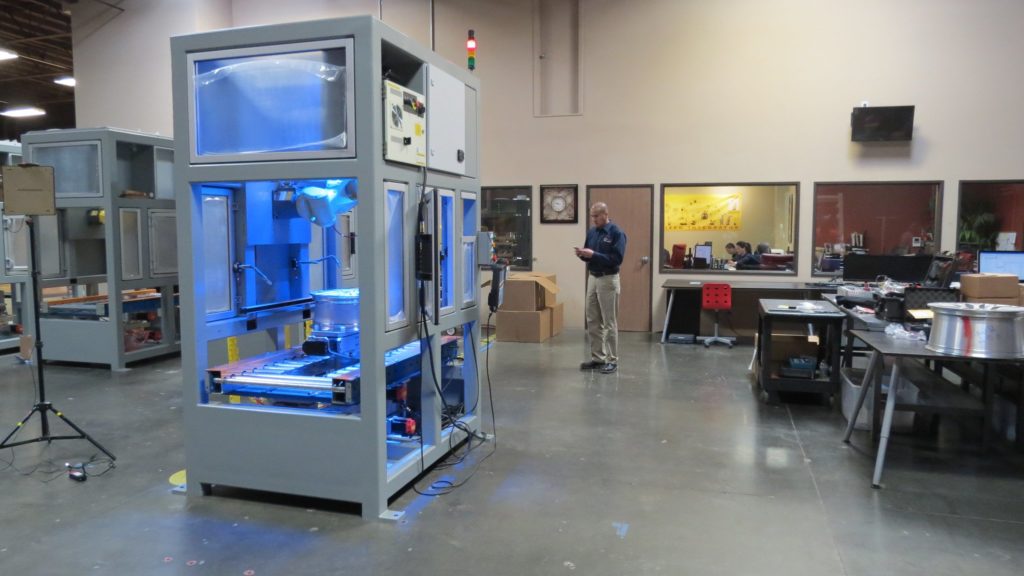
Are your issues similar? Visit our Case Studies page with new insights to uncover value centered solutions to shared automation challenges.